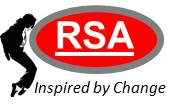
These books are written for maintenance people in industries seeking better ways of improving their equipment and assets. If you are living the day to day pressures of doing maintenance, then these books are written for you.
People become successful in life by failing. The truth is, we cannot achieve success if we do not fail. Failure is inevitable. It will happen. Success comes after failure. Just like in industries, When an equipment failure happens, we need to accept it, learn from it, challenge it and finally overcome the failure. This means that when an incident happens, we have two options, either we learn from them or just ignore them. The message of Root Cause Failure Analysis is simply to take the first option and learn from the failure. This book may be different from other books on root cause as the thoughts I have written on this book defies the conventional methods and tools for conducting a root cause. There are many versions, techniques, books, training, and consultants worldwide that explain and teach about how to conduct a Root Cause Analysis or Root Cause Failure Analysis. In fact, there is no standard or, what we can say, a universal approach on how root cause is and should be done, including this book. This book may also contradict other books on how to conduct a root cause failure investigation. I am not stating that my method or their method is right or wrong, but rather my point is that the context of this book is based on what I teach and what I believed.
The author of this book based his interpretation on his personal knowledge, experience, and former affiliation with one of the leading providers of Root Cause. I believe that uncovering the root cause is based on 100 % facts and pieces of evidence unfolded. Any investigation that is not based on evidence will not generate the root cause but only the probable or the most likely cause of the failure. The words Root Cause Analysis (RCA), and Root Cause Failure Analysis (RCFA) will be used respectively in this book. The author would prefer to use the word Root Cause Failure Analysis for equipment-related problems, while Root Cause Analysis will be used for non-equipment-related problems such as accident or safety investigation, quality defects investigation, and administrative incident investigation. Failures must not only be prevented nor predicted, but what is important is challenging failures and learning from them. Finally, this book ends on what the real message of Root Cause Failure Analysis is all about.Some of the highlights of this book includes:
- Why Failures are Important
- Why MTTR and RCFA are The Opposite of Both Worlds
- The Slow and the Fast Train
- The Golden Rule on Root Cause Failure Analysis
- Is Root Cause Failure Analysis Reactive or Proactive?
- Difference Between Analytical Problem Solving Tools and RCFA
- Evidence: The Lifeblood of Root Cause Failure Analysis
- Three Types of Evidence on RCFA
- Understanding the Physical Cause of Failures
- Understanding Human Errors<br />- Is It Possible to Eliminate Human Error in Maintenance?
- Classic Case of Human Error - The Sinking of the RMS Titanic
- Ending Our Probe on the Latent Cause of the Problem
- Classic Case of Latent Cause: The Challenger Disaster
- Decoding the Song Man in the Mirror by Michael Jackson
- Detailed Steps in Conducting an RCFA Investigation
- Different Types of Corrective Actions
- Actual RCFA Case Study
- FAQs, Tips, and Donts on RCFA
- All Failures have a Reason for Failing
- Integrating RCFA Into the RCM Process
- The Message of Root Cause Failure Analysis
Rolly, your people-focus on reliability improvement and your commitment to helping people grow through improving their understanding of equipment and of themselves come through loud and clear in the book. The workplace stories you tell will resonate with people working in operations and maintenance in every industry. I very much like that you have provided practical answers with explanations and examples of how companies can move up the path to world-class maintenance performance. You have written about TPM, RCM, and RCA with great passion and an obvious depth of knowledge and experience. I’ve learned much more about the right way to use those tools by reading your book than I ever understood before. There is no doubt that the World Class Maintenance Management - The 12 Disciplines book will become a well-thumbed reference book for me. Rolly, I’ve been fortunate to come across you and value your honest perspectives and insights on doing maintenance right. I share your desires for what maintenance can become and do for a company and hope that we can combine our efforts in the future.
This new book published in May 2020 is by far the most comprehensive maintenance management book written to date. That includes my Handbook of Maintenance Management. In 344 pages he lays out the history of maintenance management and the state of the art today. Rolly has deep experience and understanding in both RCM and TPM (an unusual combination) which adds depth to the discussion. He includes a detailed and practical glossary of keywords and their meanings. I want to make a few specific points. The assessment tool is great, and I will definitely upgrade my own assessment tool with his improvements. It covers all aspects of managing maintenance. Asset management: This is one of the best introductions to asset management and detailed rundown of ISO 5500X I've read. It shows through examples of how asset management can help the organization's effectiveness. Life cycle management is certainly part of asset management. In this case, the life cycle discussion shows definitively how most of the reliability is not under the control of the maintenance function. He says that reliability is a company's responsibility. Good graphics on the iceberg of costs to own and run a machine. Good maintenance practices may require a change in the corporation. The section on change management is well thought out and complete. Congratulations on publishing what will become the standard text in the field.
This book contains significant and relevant theory and idealism. I never read this kind of book before but it hits the core value of TPM. It is indeed maintenance quite necessary in any kind of manufacturing company. I salute for all technicalities which I don’t know it comes from before, I have learned a lot from this book. As technical personnel, I can say that it’s very much informative and vibrant. It makes a lot of sense in dealing with the alternative way of maintenance. All throughout, I was amazed by the author’s knowledge. Proud being a Filipino. Thank you for sharing this kind of book with us the author is really a mastermind on this TPM world. I absolutely enjoyed reading it even though I’m not really a reading enthusiast. I miss the Rolling Stone part which you gave the color on this book. Kudos Mr. Rolly Angeles for a good job. I now truly understand and felt being one of the maintenance team. This book has a heart and is very lively. I hope you continue to spread the meaningful story of the maintenance people. We owe you all the knowledge and being a part of this team review. Congratulations Mr. Rolly this is a heck of success. Thank you.
First I want to thank you Mr. Rolly for giving me this very rare opportunity to comment in a book and have my comment in print. At first, I was wondering where would this book lead me? Your quote “changing a system means changing a culture” captured my attention. So as I read, I already knew I need to finish reading this book. I can relate to most of what was illustrated, stated, and example in this book. They’re all true and happening. A reality. I dreamed of having a kind of maintenance organization such as those described. My only worry is that I am not in the position to implement such. It is true that this kind of approach should be top to bottom, no support from upper management means you’ll end up to nothing. I am a maintenance guy and proud to be one. But it is great to know somebody that dedicates too much time and adheres to improve the lives of maintenance people like Rolly Angeles.
Rolly Angeles
store owner
Rolly is a seasoned international maintenance and reliability consultant with over 30 years of solid experience in the field. He has been invited to different countries and has conducted reliability and maintenance training in United Arab Emirates, Qatar, India, Malaysia, Indonesia, Brunei, Thailand, Nigeria, Bangladesh, South Africa, China, and Botswana. His portfolio of maintenance training includes maintenance and reliability courses on TPM, Lubrication, Tribology, Condition-Based Maintenance, RCM, RCFA, Planned Maintenance, World Class Maintenance Management, The 12 Disciplines, Oil Contamination Control, Maintenance Indices and KPI’s, Maintenance and Reliability Management Strategies and much more. Rolly previously worked with Amkor Technology Philippines, as a TPM Senior Engineer, an industry engaged in the manufacture of Integrated Circuit products and spearheaded their Planned Maintenance organization which composed of maintenance managers and engineers.
With 30 years of solid experience, he had worked in various industries from shipping, woodworking, foundry, cast-iron machining, assembly lines, semiconductor manufacturing, and mining industry. Here was where he gained hands-on experience and understanding of both TPM and RCM respectively, a strategy from both the west and the east. His last corporate employment was in 2002 where he worked as a technical training specialist at Lepanto Consolidated Mining Industry. In 2005, Rolly retired early from the industry and decided to establish his own consulting business, RSA Reliability and Maintenance Consultancy Firm where he dedicates his time and passion to work as a maintenance consultant. He provides in-house training, consultation, and facilitation to different industries on maintenance and reliability’s best practices.